VMI and the evolution of inventory management systems
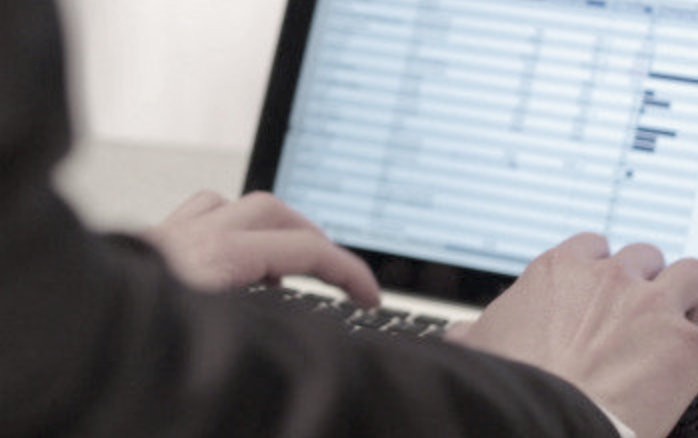
Remote inventory monitoring, with the telemetry tool, can assist in the management of supplies by the supplier itself. The practice of VMI (Vendor Managed Inventory) is already seen as a differential in the relationship between supplier and customer, and systems such as remote inventory monitoring can contribute to the efficient management of supplies with information in real time. With an eye on the competitive market, raw material suppliers and logistics operators are looking for innovative alternatives that can make a difference when it comes to customer decision.
Introduction
The practice of VMI was created in the 1990s in the United States in projects initiated by large retailers such as Walmart and has also evolved over the last few decades along with management processes. Despite being born in the retail, the technique quickly became popular and came to be seen by many suppliers of raw material in bulk.
However, in times of technological advances of wide extension, the double “price and term” does not necessarily occupy the top of the list when the subject is the management of supplies. The operational efficiency within the industrial production process passes through the reliability and, in many cases, the automation of operations. And, if the issue is trust, technology can become a strong ally of the manager and offers new clothing to IMV.
Technology for management
In the VMI concept, the supplier assumes the responsibility of managing its consumer stock, including the replenishment process. What used to be called “consigned stock” now fits into the context of a business environment with a higher level of collaboration, with another dynamic and using telemetry.
If, by conventional methods, it was necessary for someone with paper and pen to periodically measure and record the stock of raw material before making a new request, the current mechanisms allow a sensor installed in the tank or silo to constantly measure the level of the available inventory and electronically transmit information through the 3G / GSM cellular internet to a system programmed to identify when the stock is below expected, according to previously agreed levels between supplier and customer. This gives the vendor the automatic product reset alert. This telemetry feature gains new proportions and facilitates the flow in the business VMI model when it is associated with the monitoring system, which has a programmed intelligence to treat the data received by the sensors and turn them into information and technical subsidies for making as the following graphs demonstrate. What’s more, state-of-the-art technology still provides real-time access to the system from any computer, cell phone or tablet.
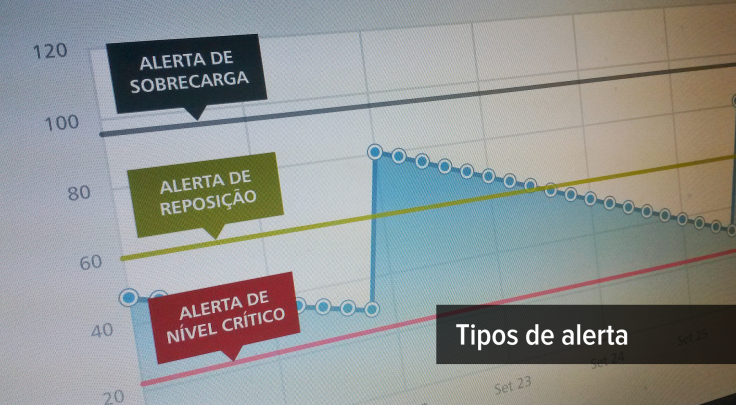
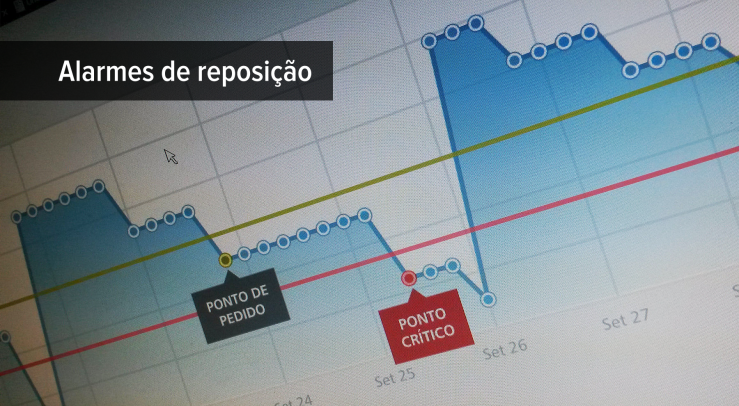
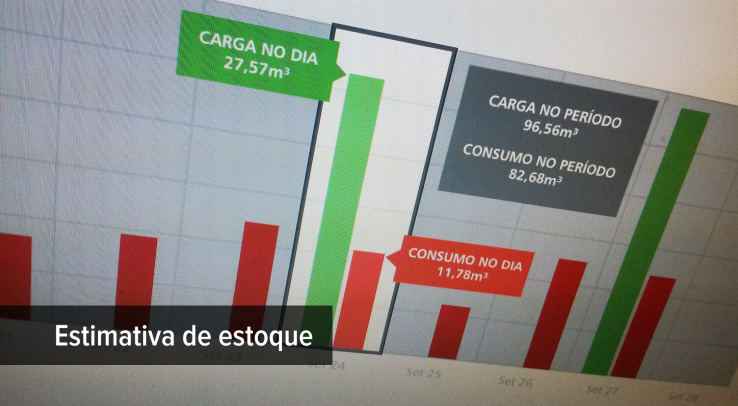
VMI does not simply mean visiting a customer a few times a month to replenish their materials based on agreed levels. The difference is that the supplier monitors the consumer’s sales and inventory information, and the VMI is defined as an agreement between both parties, in which consumers give suppliers the authority and responsibility for the automatic resupply of their materials. Thus, consumers do not need to send purchase orders to their suppliers, relying on the delivery of the necessary and sufficient quantities of inventory to meet their consumption. This is a more advanced version of continuous refueling, where suppliers can gradually reduce inventory levels as long as they maintain all levels of service.
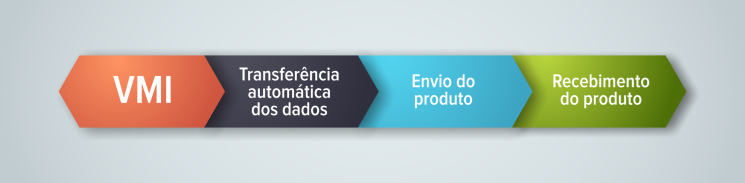
By this mechanism, the customer and supplier have the same perception about the cycle time of the order, that is, the cycle begins when the inventory level reaches the order point and ends with the formal delivery and receipt of the product at the place of destination. Moreover, if the customer begins to consume more or less quickly certain raw material, refueling alarms accompany this demand and become more or less frequent. Another positive factor is the elimination of price and credit negotiation steps between supplier and customer, since refueling occurs on predetermined bases between the two parties. Alongside this comes the sophistication of inventory measurement and order preparation / transmission, which occur automatically, reducing the procurement process cycle.
For the supplier, this alternative demonstrates a competitive differential and an improved logistics standard.
Beside this, if the customer or supplier still makes use of integrated internal management systems (such as SAP, ERP, among others), the remote monitoring system can also integrate with these tools, improving administrative processes and operations.
The whip effect
The vast majority of companies manage their inventories from an internal and isolated perspective, without reflecting on their effects as a whole, although ideally all the links in the supply chain would always have on hand real and online information on the demand generated from a stock management system.
Therefore, the adoption of collaborative planning and automatic replenishment practices, such as VMI, is a great tool to reduce the popular “whip effect”, in which the fluctuations of the supplier’s demand are much larger than the actual demand In the client. And supply chains are extremely prone to the “whip effect”, which has a negative impact, increases the level of safety stocks and / or a loss of service level and even causes a lack of products. Uncertainty is most responsible for the “whip effect”, which can precisely be reduced by the IMV mechanism, since the supplier itself is in charge of making available the necessary raw material to the consumer to be used when and as needed, acting as a kind of “extension” of the customer’s material management area.
Service model
With telemetry (automatic metering of tanks or silos), the raw material replenishment cycle becomes faster and more programmed, in addition to reducing the risk of rupturing the customer’s production chain. This cycle can happen in two formats:
- Inbound VMI: The raw material stock management at the customer’s plant is done by the supplier.
- Outbound VMI: Product inventory management at the customer’s plant is done by your own staff. This is the case, for example, of a company that has several factories in different regions, or in remote locations, and has a centralized purchasing system.
These service dynamics have already been used in different segments of the industry.
Benefits
The client inventory manager in the VMI model can, above all, gain time to devote to business strategies, since the basic tasks are automated within the remote monitoring system. However, other benefits can be highlighted:
- Unified view of inventories.
- More accurate planning of the supply chain and logistics.
- Control of raw material demand.
- Gains in efficiency and effectiveness (operational, logistics and production).
- Automated inventory management, minimizing the risk of disruptions in the production process.
- Accuracy of information and inventory data, eliminating communication failures.
- Frequent alerts for refueling in case of high consumption of products.
- Reduced transportation costs.
- Reduction of the number of carts in the waiting yard.
- Loyalty between supplier and customer.
Final considerations
The basic concept for VMI is the integration of information between supplier and customer. And it is with this same principle that the system of inventory monitoring is built at a distance: integrated and real-time information guarantees an improved supply chain management that can be done by the customer, the supplier and the logistic operator at the same time, from telemetry allied to an intelligent (mobile, agile and reliable) system that interprets the data according to parameters pre-established by the users and provides subsidies for decision making at the right time.
In the search for a differentiated and long-term business relationship, the cost-benefit of implementing a remote monitoring system is usually extremely attractive considering the benefits that the company (be it supplier, customer or logistic operator) will be able to enjoy.
References
AMMER, D. S. Administração de Material. Rio de Janeiro: Livros Técnicos e Científicos,1979. (p. 02).
BALLOU, R. H. Gerenciamento da Cadeia de Suprimentos: Planejamento, organização e logística empresarial. Porto Alegre: Bookman, 2001.
DIAS, M. A. P. Administração de Materiais: Uma abordagem Logística. São Paulo: Editora Atlas, 1983.
PEREIRA, Suelen Elizabete Hopp – Utilização da Prática de VMI no Abastecimento de Oxigênio de um hospital público/Suelen Elizabete Hopp Pereira – 2012 (p. 33-34-36).
http://ogerente.com/logisticando/2007/03/12/processo-para-implementacao-do-vmi/ Acesso em 12/09/2014.
http://pt.wikipedia.org/wiki/VMI Acesso em 15/09/2014.
http://www.simpep.feb.unesp.br/anais/anais_13/artigos/740.pdf Acesso em 17/09/2014.
http://www.12manage.com/methods_vendor_managed_inventory_pt.html Acesso em 17/09/2014.
http://pt.wikipedia.org/wiki/Continuous_Replenishment_Program Acesso em 17/09/2014.
https://www.netvmi.com.br Acesso em 18/09/2014.